六大航天先進復合材料研究進展
來源:本站 時間:2024-04-24 00:00:00
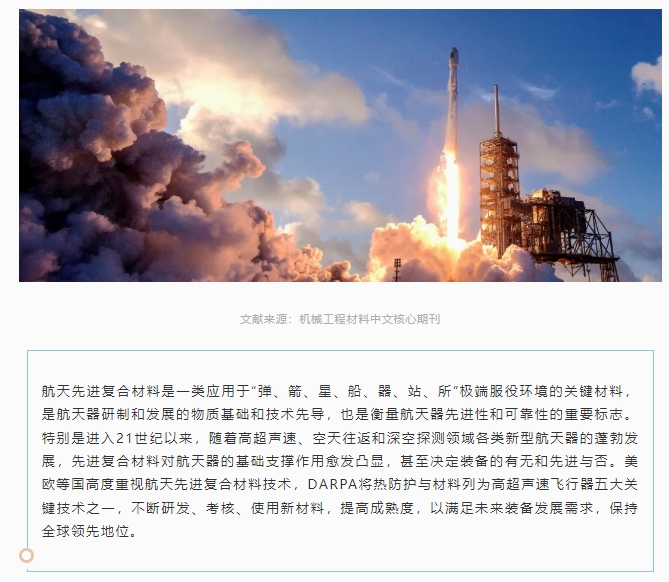
隨著航天器的速域和空域不斷拓展,先進復合材料研究的深度和廣度也日益增強。一方面,復合材料需要在極端復雜環(huán)境中高可靠服役,具有復雜的組分和結構,對材料的輕量化、耐溫性、多功能一體化等性能要求極高,需要不斷發(fā)展新的高性能材料。另一方面,需要深入研究復合材料材料在極端環(huán)境中組分、結構及性能的演變規(guī)律、多物理化學場與材料耦合作用等,提高對材料服役性能的認識。因此,面向未來航天器需求和復合材料自身技術發(fā)展,亟需在理論、方法和技術等方面實現(xiàn)創(chuàng)新。
陶瓷基熱結構材料是由陶瓷基體和纖維增強相組成的復合材料,具備高比強度、比模量及優(yōu)異的高溫力學、抗氧化和耐燒蝕等性能,是航天器理想的熱結構材料。美歐等國早就認識到陶瓷基復合材料的重要應用價值。通過一系列研究計劃的持續(xù)支持,在高品質原材料、復合材料設計、制備工藝及工程應用方面取得了諸多突破。例如,2015年2月,歐洲IXV試驗飛行器飛行成功,其熱防護系統(tǒng)頭錐、迎風面大面積、翼前緣和體襟翼均采用C/SiC復合材料,可以滿足超過1600℃的服役要求,薄壁異形構件尺寸達到了米量級,體現(xiàn)出很高的制備工藝水平,技術成熟度較高。近年來,我國在陶瓷基熱結構材料領域取得了長足進步,突破了大尺寸異形薄壁C/SiC熱結構材料的設計于制備關鍵技術,并實現(xiàn)了工程化應用。同時,針對陶瓷基熱結構輕量化、耐高溫和低成本等不同需求,發(fā)展了C/SiBCN、C/SiHfBCN及C/SiCN等新型陶瓷基熱結構材料。采用前驅體浸漬裂解工藝制備的C/SiBCN材料,比C/SiC具有更優(yōu)異的高溫抗氧化性能。研究發(fā)現(xiàn),SiBCN陶瓷在1400℃下空氣中的氧化動力學常數(shù)Kp明顯低于SiC陶瓷,如圖1所示。此外,C/SiBCN復合材料室溫下彎曲強度489 MPa,在1600℃彎曲強度仍達到450 MPa以上。為進一步提升材料耐溫性能,將SiHfBCN納米復相超高溫陶瓷引入到C/SiC基體中,研制出C/SiC-SiHfBCN復合材料,室溫拉伸強度大于300 MPa,彎曲強度大于450 MPa;2 000℃拉伸強度達到120 MPa,彎曲強度達到200 MPa。針對低成本陶瓷基熱結構需求,研制了新型SiCN前驅體,兼具高陶瓷產(chǎn)率和低成本優(yōu)點。采用該前驅體研制的C/SiCN復合材料成本更低。圖2為C/SiCN復合材料的的力學性能。室溫拉伸強度和彎曲強度分別達到了230 MPa和380 MPa,且到1400℃時力學性能無明顯衰減。 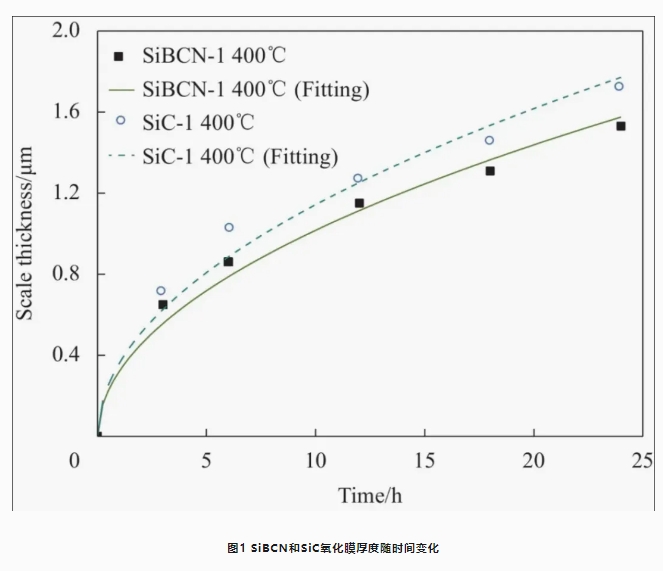
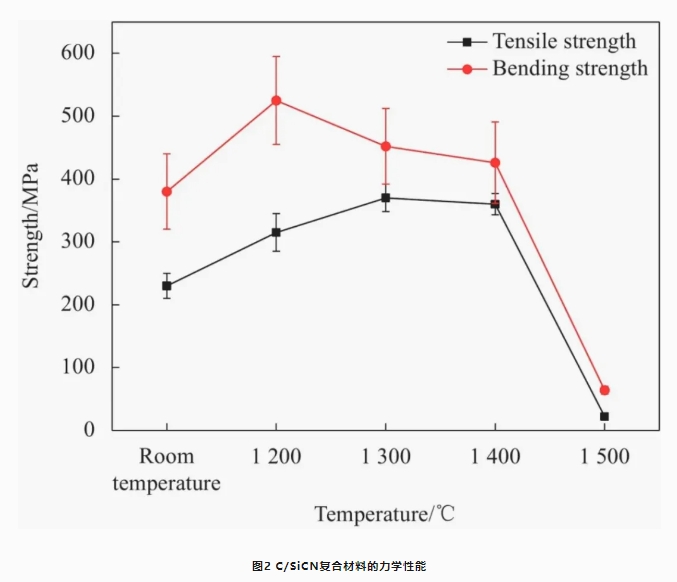
陶瓷基熱結構是新型飛行器的共性關鍵技術。研究新型耐高溫纖維及先驅體、研制高性能熱結構材料,發(fā)展先進制備工藝,降低陶瓷基熱結構制備周期及成本,將是陶瓷基熱結構重要的發(fā)展方向。超高溫低燒蝕防熱材料主要用于航天飛行器的端頭、前緣等熱環(huán)境嚴苛部位?;谔祭w維增強的改性碳基或超高溫陶瓷基復合材料是超高溫低燒蝕防熱材料的重要體系。C/C復合材料在惰性條件下具有優(yōu)異的化學穩(wěn)定性與力學性能,但在400 ℃以上發(fā)生氧化,制約了在高溫有氧環(huán)境下的使用。通過在碳基體中添加抗氧化改性組元,可以顯著提高C/C復合材料的抗氧化性能與抗燒蝕性能。漿料浸漬法可能是在碳纖維預制體引入陶瓷組元最常用的方法。研究發(fā)現(xiàn),陶瓷顆粒與纖維的直徑比例對實現(xiàn)陶瓷顆粒的致密堆積非常重要。Binner等采用真空浸漬法在2.5D碳纖維織物中引入HfB2漿料,得到碳纖維增強HfB2復合材料。氧-乙炔焰考核發(fā)現(xiàn),當不同粒徑的HfB2顆?;旌鲜褂脮r,復合材料在氧-乙炔焰考核時表現(xiàn)出最好的抗燒蝕性能,圖3為材料考核后的表面狀態(tài)。此外,前驅體浸漬裂解、反應熔滲法也可用來制備低燒蝕防熱材料。超高溫低燒蝕防熱材料的微觀結構與制備工藝緊密相關,進而決定材料性能。Lazzeri指出,采用兩種或以上復合工藝可能是獲得高性能低燒蝕防熱材料的潛在方法。
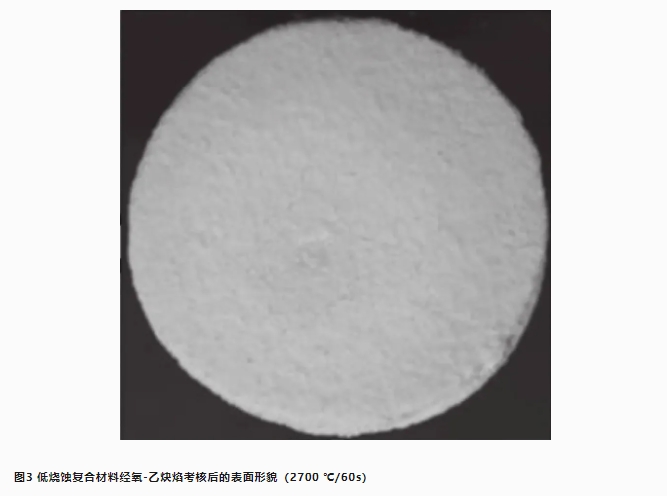
國內在C/C復合材料基體改性方面開展了大量研究工作。通過物理摻雜、化學絡合等工藝方法在碳纖維織物中引入Hf、Zr、Ta、W等難熔金屬組元的碳化物、硼化物及硅化物,制備出超高溫本體抗氧化C/C復合材料,抗氧化燒蝕性能較C/C復合材料提高60%以上,圖4是材料燒蝕后的形貌。此外,還通過在C/C復合材料內部引入多組元,制備了具有雜化基體的C/C-ZrC-SiC、C/C-HfC-SiC復合材料。通過陶瓷粉體和前驅體的組合使用,不但實現(xiàn)了多相組元的高效均勻引入,而且使材料具有良好的力學性能,彎曲強度和壓縮強度均達到130 MPa以上。在室溫到2500 ℃以上典型環(huán)境風洞試驗考核中表現(xiàn)出良好的抗燒蝕性能,實現(xiàn)了型號成功應用。
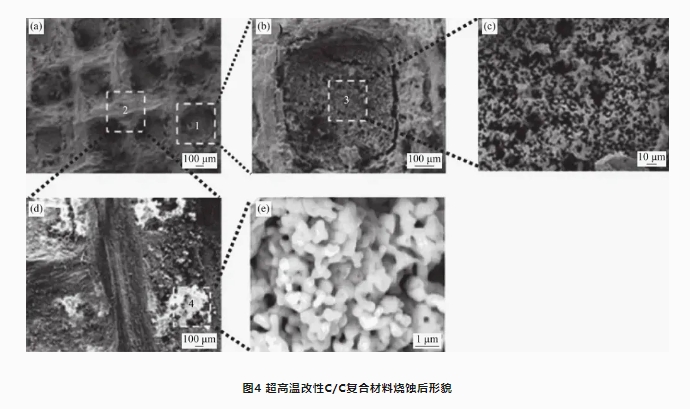
在C/C復合材料中引入抗燒蝕組元是制備超高溫低燒蝕防熱材料的有效方法。材料的力學性能和抗燒蝕性能與材料組分和微觀結構緊密相關。通過優(yōu)化材料組元及引入方式,提高組元分布均勻性、減少顆粒團聚、降低裂紋缺陷、提高組分熱匹配等措施研制耐溫等級更高的超高溫低燒蝕防熱材料是該領域的發(fā)展重點。
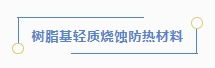
樹脂基燒蝕防熱材料是一種為適應航天器熱環(huán)境而研制的功能復合材料,用以防護飛行器結構在氣動熱環(huán)境中免遭燒毀破壞,具有防熱效率高、比熱容大、熱導率低、制備周期短、成本低的特點。近幾年,隨著新型飛行器技術的發(fā)展,樹脂基燒蝕防熱材料輕量化及多功能化技術迅速發(fā)展,成為該類材料的研究熱點,推動了技術進步,拓展了應用領域。NASA針對深空探測器熱防護需求,設計并研制了具有梯度結構的樹脂基輕質燒蝕防熱材料(HEEET)。HEEET具有三維編織的雙層結構,外層為燒蝕層,增強體為碳纖維;內層為隔熱層,增強體為碳纖維和酚醛纖維。燒蝕層和隔熱層之間通過纖維連接在一起,形成整體式結構,然后在纖維孔隙中填充具有多孔結構的酚醛樹脂,得到HEEET防熱材料。圖5(a)顯示了HEEET材料表層和內層的梯度結構。HEEET既具有良好的抗燒蝕性能,又具有優(yōu)異的隔熱性能,成為未來深空探測器具有應用潛力的一種新材料。圖5(b)是HEEET熱防護材料典型構件。Chang等將3D打印技術引入輕質燒蝕防熱材料的制備過程,研制出具有梯度結構的輕質防熱材料,以期能夠最大程度降低材料的質量,如圖6所示。該技術還在進一步研究中。
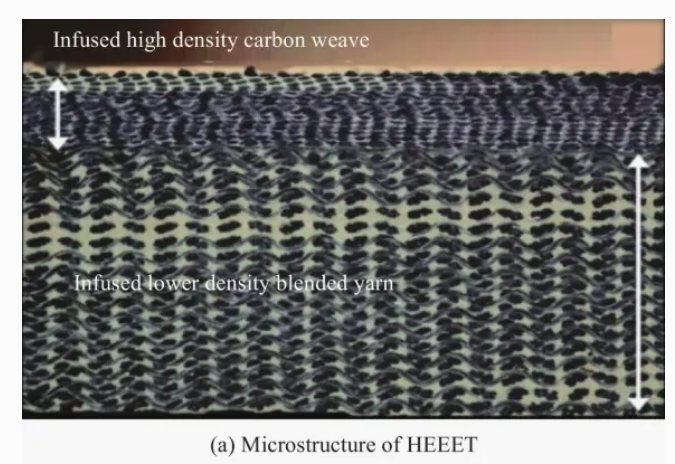
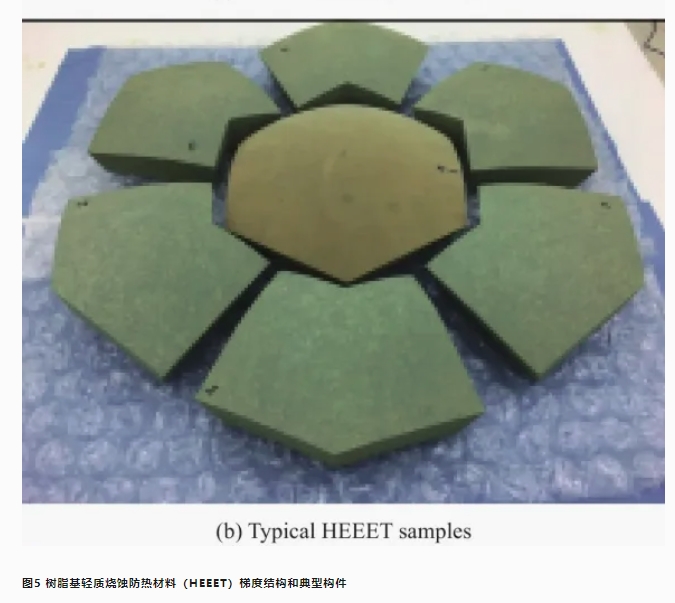
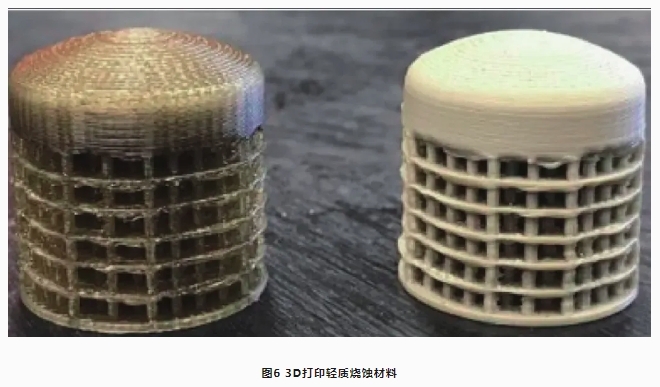
國內也發(fā)展了幾類輕質燒蝕防熱材料,并成功應用于嫦娥五號、天問一號等空間探測器,形成了成熟的材料系列。此外,國內還發(fā)展了多功能樹脂基輕質防熱材料。通過對纖維增強體和樹脂基體的設計,將防熱、隔熱、吸波多重功能融合,能夠滿足飛行器關鍵部位防熱、隔熱和高溫電磁隱身的功能,具有多重功能無界面融合且協(xié)同作用的特點。典型材料密度為0.5 g/cm3,室溫熱導率為 0.045 W/(m·K),除具有良好的防熱性能外,在2~18 GHz寬頻范圍內還具有較好的吸波性能,圖7是防熱隱身材料示意圖。
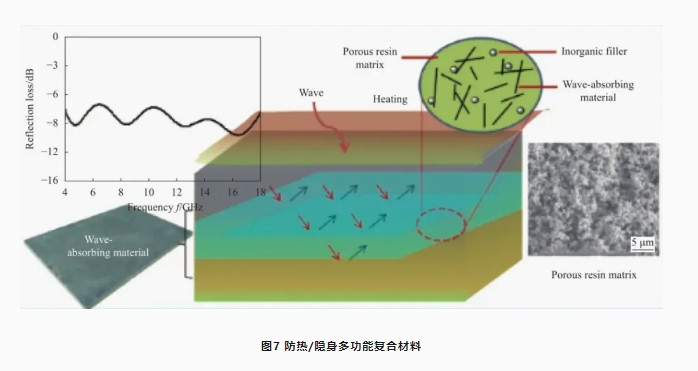
隨著新型飛行器的發(fā)展,實現(xiàn)樹脂基燒蝕防熱材料的輕量多功能兼容與集成化,滿足材料不同使用場景的需求,實現(xiàn)熱防護系統(tǒng)精細設計與精準制造,樹脂基輕質防熱材料將發(fā)揮更重要的作用。
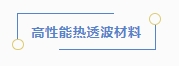
高性能熱透波材料用于飛行器天線罩(窗),早期主要以石英陶瓷、氧化鋁陶瓷、微晶玻璃等為主,后來發(fā)展了可靠性更高的石英纖維增強氧化硅復合材料。隨著飛行器速度越來越高,飛行時間越來越長,對高溫長時透波材料的需求也越來越迫切,氮化物纖維增強陶瓷復合材料成為高溫透波材料的研究熱點。日本東亞燃料公司以氮化硅纖維為增強體,全氫聚硅氮烷陶瓷前驅體為基體,制備了氮化硅纖維增強陶瓷復合材料,材料室溫彎曲強度為184 MPa,模量102 GPa,1000 ℃的強度達到191 MPa,模量92 GPa。國內也開展了氮化硅纖維增強陶瓷復合材料的研究。Zou等和Yang等報道了Si3N4f/BN復合材料性能,室溫下材料的彎曲強度約為133 MPa,但隨溫度的升高,彎曲強度下降,1300 ℃時彎曲強度減小至約73 MPa。航天材料及工藝研究所突破了氮化硅纖維增強陶瓷復合材料及米量級天線罩制備技術,研制的復合材料具有優(yōu)異的力學性能、抗燒蝕性能及介電性能,材料室溫拉伸強度大于70 MPa,1200 ℃拉伸強度大于50 MPa,1400 ℃拉伸強度大于40 MPa,典型環(huán)境下的線燒蝕速率顯著低于石英復合材料,且介電性能穩(wěn)定,有望用做高溫服役環(huán)境的天線罩材料,如圖8所示。
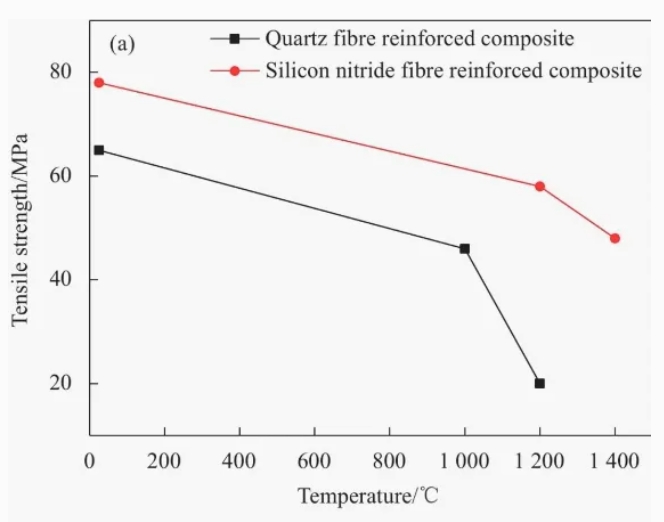
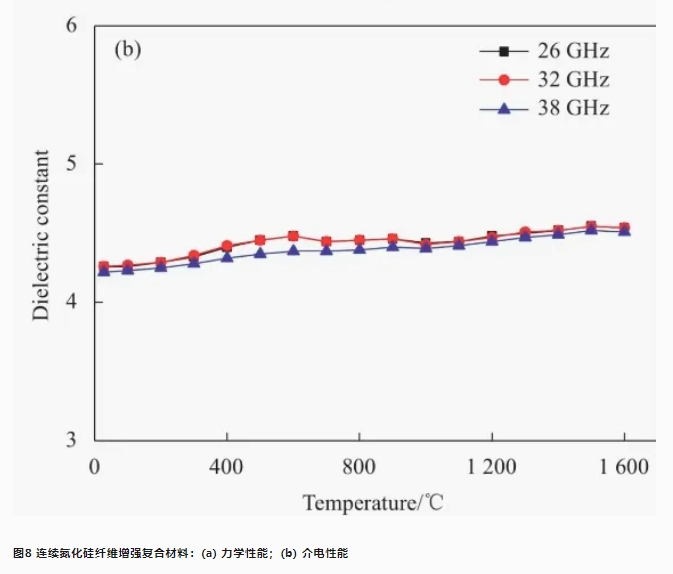
除Si4N3纖維增強復合材料外,SiBN、BN等纖維增強復合材料也是潛在的高溫透波材料,但由于纖維尚未實現(xiàn)大批量制備,復合材料性能研究結果較少。新型纖維的出現(xiàn)可為未來高性能熱透波新材料的研究提供關鍵原材料支撐。可在更高溫度下使用的熱透波材料是該領域發(fā)展的重要方向。
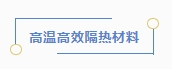
高超聲速飛行器飛行速度不斷提高,飛行時間更長,對高溫高效隔熱材料的需求更加迫切?,F(xiàn)有成熟隔熱材料,如陶瓷瓦、隔熱氈、氧化物納米隔熱材料的使用溫度已不能滿足未來飛行器要求。碳及碳化物多孔隔熱材料在惰性環(huán)境中具有優(yōu)異的熱穩(wěn)定性和隔熱性能,成為目前國內外超高溫隔熱材料的研究重點。碳纖維氈、碳泡沫等是最常見的高溫隔熱材料,作為窯爐保溫材料早已實現(xiàn)商品化生產(chǎn),并廣泛應用,但其隔熱性能不佳。近年來,以碳氣凝膠為代表的多孔隔熱材料引起研究者的高度重視。德國巴伐利亞應用能源研究中心的科學家首次較全面的報道了碳氣凝膠的隔熱性能,測試得到1500 ℃的熱導率為0.12 W/(m·K),并通過計算得到2500 ℃的熱導率為0.16 W/(m·K),隔熱性能是碳氈的2~5倍,受到廣泛關注。美國空軍研究實驗室對以抗氧化碳/碳為外面板,碳氣凝膠為內部隔熱層,總厚度為38 mm的組合隔熱結構進行熱試驗考核,防熱結構表面溫度 1927 ℃,加熱時間15 min后,背面溫度僅為611 ℃。證明了該防隔熱結構在超高溫下具有較好的隔熱性能和抗熱震性能,并推薦在防熱材料與結構中應用。2018年美國發(fā)射“帕克”太陽探測器,為抵御日冕層高溫,探測器正對太陽的方向安裝了耐高溫的防熱罩,見圖9。資料顯示,該防熱罩主體為碳泡沫,直徑約為2.44 m,厚度約為114 cm,是迄今為止報道的尺寸最大的碳質隔熱材料構件,體現(xiàn)出極高的制造工藝水平。
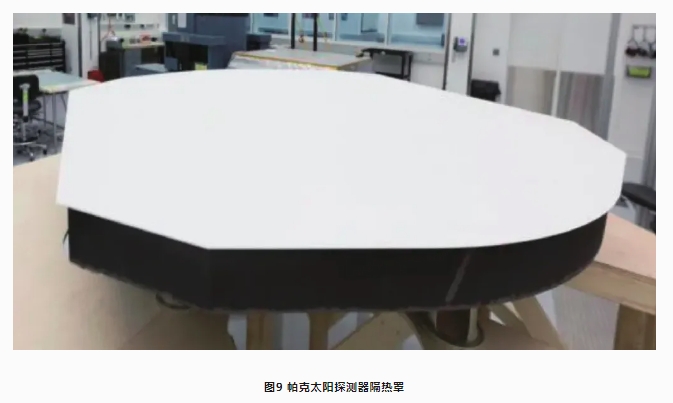
日本宇宙航空開發(fā)研究機構認為碳質隔熱材料有潛力用于在深空探測器的高溫防隔熱系統(tǒng),并設計了“抗氧化碳/碳+碳泡沫+鋁蜂窩”三層組合的輕質防熱結構。其中碳泡沫密度為0.18 g/cm3,室溫熱導率約為0.14 W/(m·K)。在電弧風洞試驗考核時,表面最高溫度達到2000 K,具有較好的熱穩(wěn)定性和隔熱性能,綜合性能突出。國內Li等報道了纖維增強碳氣凝膠隔熱材料的性能,見圖10,密度為0.6 g/cm3的碳氣凝膠復合材料壓縮強度可達80 MPa,厚度為7.5~12 mm的材料在1800 ℃氧-乙炔焰加熱900 s的考核條件下,背面溫度為685~778 ℃,顯示出優(yōu)異的性能。

碳質超高溫隔熱材料在飛行器高溫隔熱領域已經(jīng)展現(xiàn)出重要的應用價值。發(fā)展該類材料的微觀結構調控方法,提升優(yōu)化材料性能,建立大尺寸材料的制備工藝,進行典型環(huán)境中的試驗考核是碳質超高溫隔熱材料的重要研究方向。
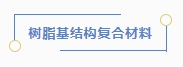
樹脂基結構復合材料具有高的比強度、比模量,能夠實現(xiàn)運載火箭、衛(wèi)星、導彈等的結構輕量化,其用量也是衡量航天器結構先進性的指標之一。經(jīng)過多年發(fā)展,目前已經(jīng)形成了基體為環(huán)氧樹脂、雙馬樹脂和聚酰亞胺樹脂為代表結構復合材料系列。隨著近年來高性能碳纖維和新型樹脂的發(fā)展,樹脂基結構復合材料的承載性、工藝性、穩(wěn)定性等也逐漸提高。圖11為日本東麗公司開發(fā)的NANOALLOY®納米尺度共混技術,研制出新型高強高模樹脂基體,顯著提升復合材料的性能。
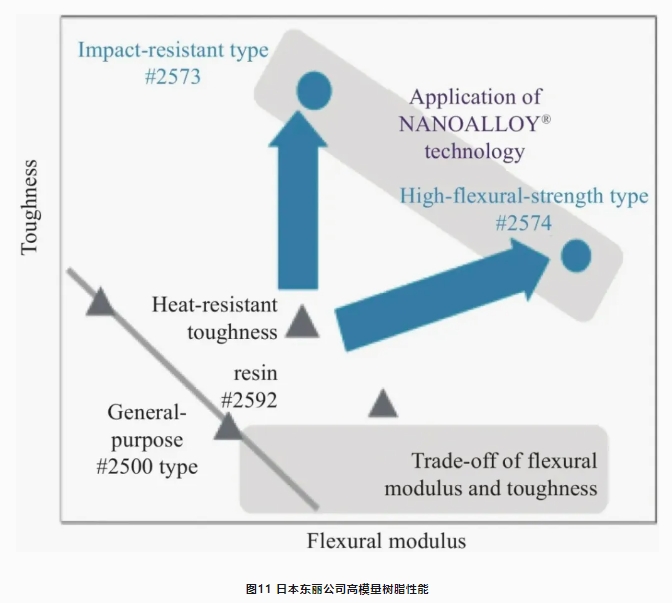
雙馬來酰亞胺樹脂工藝性好,國外開發(fā)了豐富的樹脂品種,形成了系列化。美國Narmco公司研制出5250雙馬樹脂,以其為基體的復合材料具有優(yōu)良的耐高溫、韌性和耐濕熱性能,IM7/5250復合材料已在X-37 B空天飛行器機身蒙皮、梁等部件使用,通過多次長時飛行試驗的驗證。聚酰亞胺樹脂是耐溫等級最高、應用最廣泛的高溫結構樹脂。在聚酰亞胺分子結構中引入含硅單體,可以顯著改善樹脂的工藝性,降低熔體黏度,同時提升其熱氧化穩(wěn)定性。Hout等采用多面體聚倍半硅氧烷單體替代毒性的二氨基二苯甲烷(MDA)單體,改善了樹脂的耐濕熱性,且高溫下表層形成二氧化硅保護層,提高了材料熱氧化穩(wěn)定性。美國Performance Polymer Solution公司研制的P2SI® 900 HT有機無機雜化聚酰亞胺樹脂使用溫度達到了538 ℃,高溫性能優(yōu)異。在航天型號牽引下,我國樹脂基結構復合材料進步明顯,突破了一系列高性能樹脂基結構復合材料技術,開展了第三代先進環(huán)氧樹脂基結構復合材料研究,研制出高強高模樹脂603 HM樹脂,模量達到6.0 GPa,采用該樹脂研制的復合材料壓縮強度達到2100 MPa,壓拉比達到了0.75。針對短時高溫應用場景,開展耐280 ℃雙馬樹脂及復合材料的研制,復合材料280 ℃強度保持率在50%以上,模量保持率在80%以上?;谟袡C無機雜化的分子設計思路,研制出第四代耐500 ℃聚酰亞胺樹脂及復合材料,500 ℃彎曲強度和模量保持率分別在55%和85%以上,性能優(yōu)異。針對未來航天器需求,樹脂基結構復合材料應重點發(fā)展新型樹脂、多尺度強韌化、樹脂協(xié)同增剛增強及界面匹配、碳纖維復合材料壓拉比調控等,研發(fā)新一代樹脂基結構復合材料。發(fā)展樹脂基復合材料結構的自動化制造技術,進一步提升復雜構件自動化成型及加工裝配水平。
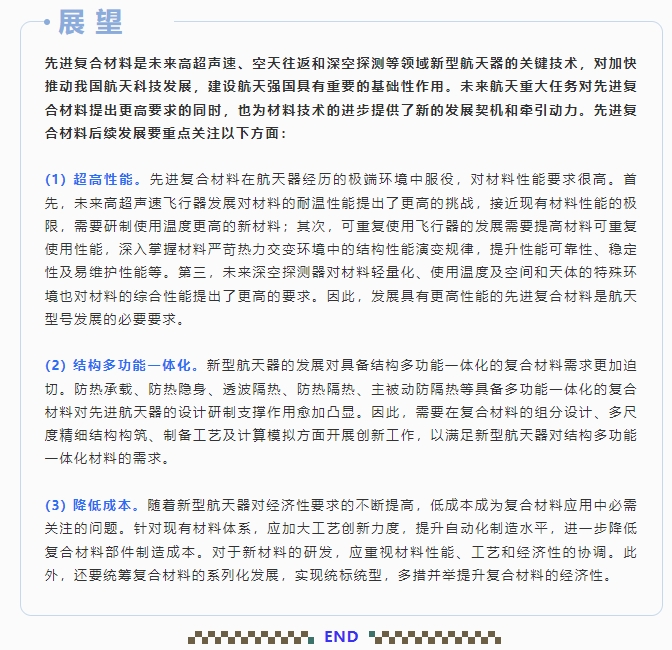
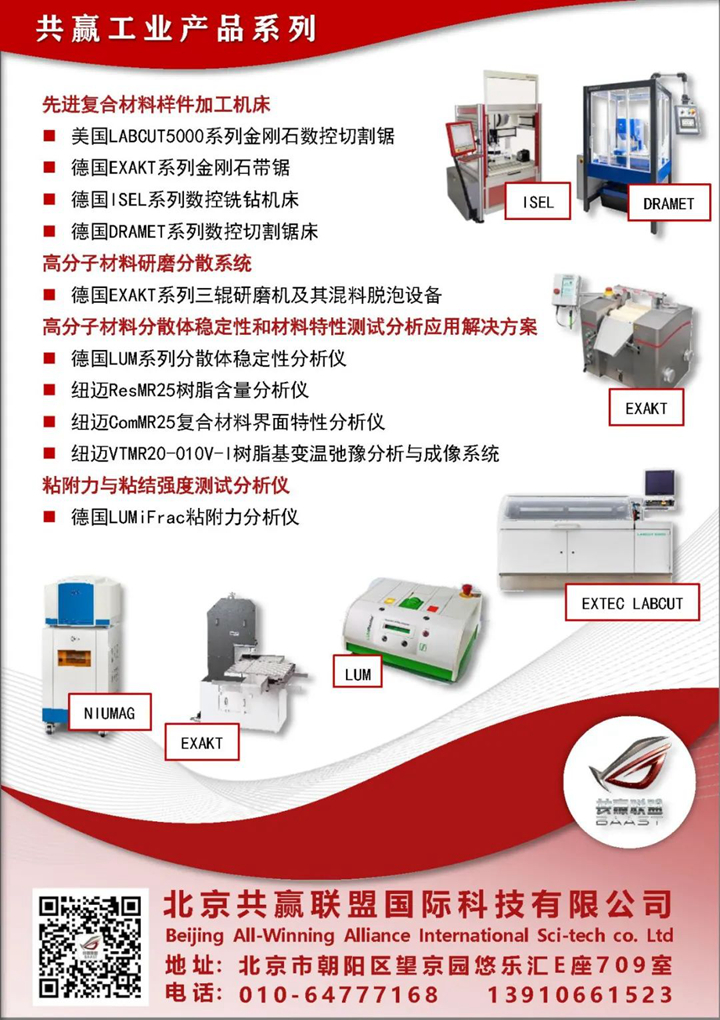